Process Optimization
Manufacturing companies often know that they’re operating below their ultimate production capacity, but struggle with how to overcome their process challenges. These challenges include having inefficient workflows that waste time and resources, quality control issues, and hidden bottlenecks that impact workflow and cause delays. Overcoming these challenges is essential for driving performance and achieving operational excellence.
Inefficiencies and Waste: Cumbersome and complex processes lead to wasted time, resources, and effort, diminishing productivity and eroding profitability.
Quality Control Issues: Inconsistent processes can create defects and errors, tarnishing the company’s reputation and reducing customer satisfaction.
Underutilized Capacity: Unused capacity reduces production efficiency and scalability, limiting growth opportunities.
Lack of Adaptability: Rigid processes make it difficult to respond quickly to changing market demands and customer needs, resulting in missed opportunities.
Hidden Bottlenecks: Undetected process bottlenecks impede workflow and delay production, leading to increased lead times and delivery delays.
Process Optimization initiatives use the fundamental principles of Lean to eliminate waste, reduce variation, improve quality, and increase production capacity.
-
- Enhanced Efficiency: Streamlined processes have less waste and optimized resource utilization, boosting productivity and operational efficiency.
-
- Increased Capacity Utilization: Optimization efforts unlock previously untapped capacity, enabling companies to meet growing demand and scale operations sustainably.
-
- Greater Flexibility: Agile processes facilitate rapid adaptation to market changes, enabling companies to seize new opportunities and stay ahead of the competition.
-
- Maximized Performance: With optimized processes in place, manufacturing operations achieve peak performance, driving sustainable growth and performance.
-
- Improved Quality: Standardized processes and quality control measures minimize defects and errors, enhancing product quality and customer satisfaction.
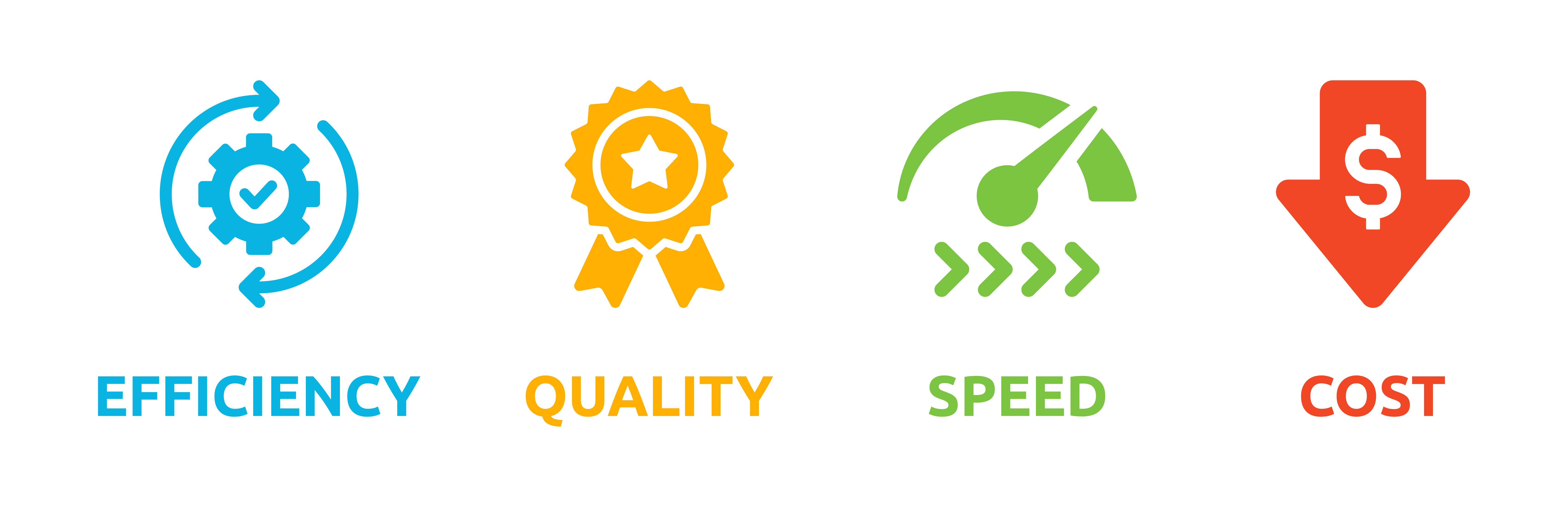
The Process Optimization Process: From Analysis to Action
1. Conduct Time and Motion Studies: Conduct detailed observations of work processes to identify inefficiencies and opportunities for improvement.
2. Identify Waste: Use Lean principles to identify and eliminate various forms of waste, such as overproduction, waiting, and unnecessary motion.
3. Value Analysis: Evaluate processes to identify non-value added activities and streamline operations to focus resources on activities that directly contribute to customer value.
4. Capacity Utilization: Assess current capacity levels and develop strategies to optimize resource utilization and maximize production output.
5. Continuous Improvement: Create a culture of continuous improvement, where processes are regularly reviewed, refined, and optimized to drive ongoing performance gains.
Maximize Capacity and Efficiency with Process Optimization
Book a free Discovery Call today and explore what’s possible with lean for your organization.