Process Mapping
In many manufacturing companies, the lack of clear, documented processes is the source of the chaos in their production operations including operational inefficiencies , quality issues, bottlenecks, difficulties training new staff, and being unclear about process improvement opportunities.
Operational Inefficiencies: Unclear processes result in wasted time and resources as employees struggle to navigate complex and undocumented workflows.
Quality Control Issues: Without standardized processes, maintaining consistent quality standards becomes challenging, leading to errors, defects, and unhappy customers.
Bottlenecks and Delays: Undefined processes can lead to bottlenecks and delays in production, causing disruptions and extending delivery timelines.
Training Challenges: New employees have trouble understanding and following undefined processes, leading to longer onboarding times and lower productivity.
Missed Opportunities: Without clear processes in place, opportunities for improvement and optimization are often overlooked, limiting the company’s ability to innovate and grow.
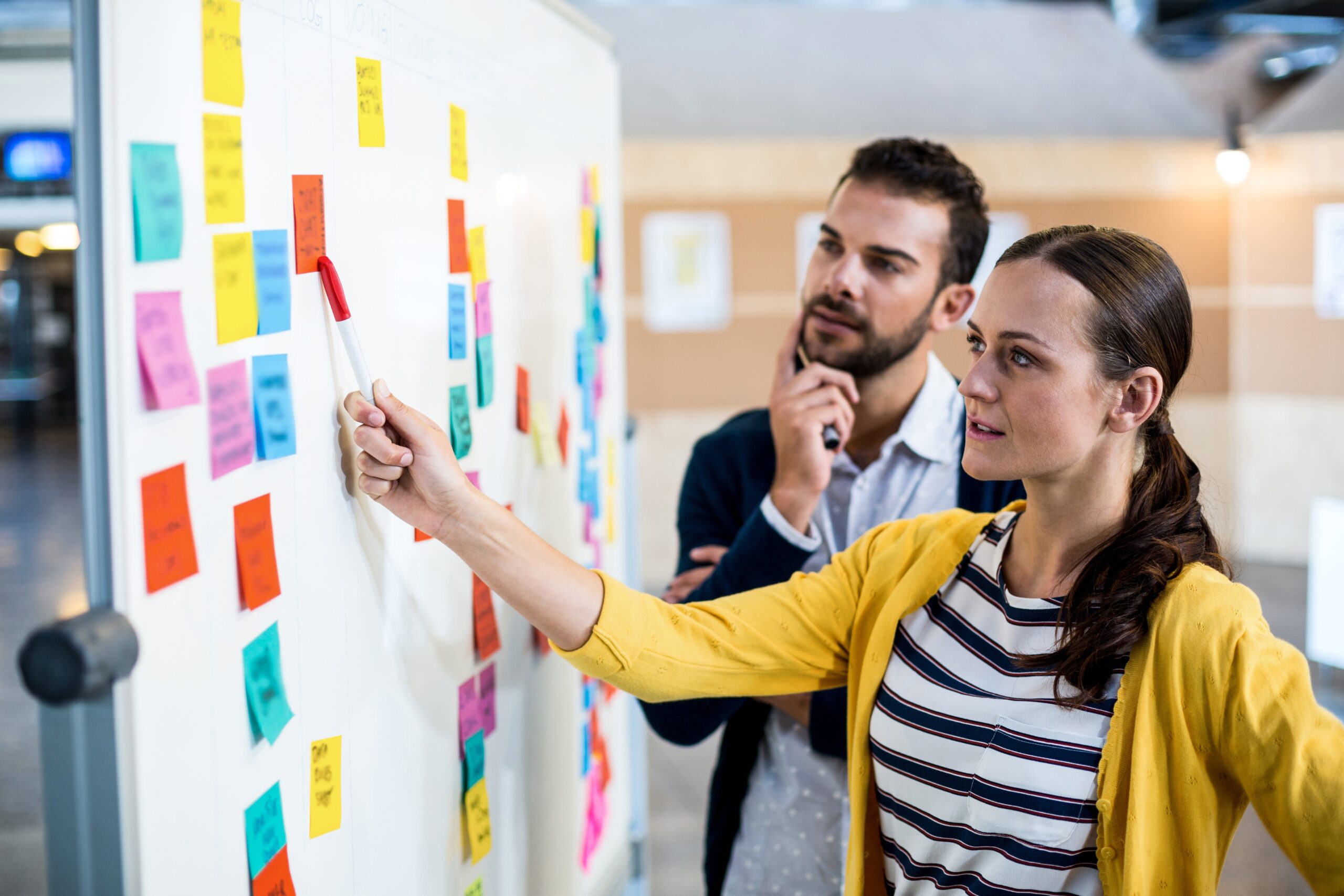
Process Mapping is a systematic approach to visualizing and documenting each step of a process, to create a map that displays how the process works from start to finish.
Visualize: Document each step of the manufacturing process using sticky notes and markers to capture the Current State of the process.
Analyze: Identify process waste, inefficiencies, production bottlenecks, and process improvement opportunities.
Standardize: Establish standardized work procedures and processes to ensure consistency and quality across all operations.
Communicate: Share the process map with employees at all levels of the organization, to create a shared understanding of how the business operates.
Continuous Improvement: Use process mapping as a tool for ongoing improvement, regularly reviewing and updating the maps to reflect changes in processes, technology, and business requirements.
Transform Your Business Processes
Streamline your workflows, elevate process efficiency, increase quality, empower
your people, and drive your continuous improvement efforts with Process Mapping.
Book a free Discovery Call today and unlock the full potential of your operations.