Lean Business Assessments
Need to Streamline Your Processes But Don’t Know Where to Start?
Good news, you’ve found the right place.
In today’s economy it’s more important than ever to maintain a competitive edge. Rising costs, supply chain breakdowns, budget constraints – common frustrations for small and mi-size manufacturing operations. You’re clear something needs to change but where should you start? How can you do more with the same resources?
Ever wish you could be efficient and effective in your business but feel stuck being overwhelmed and frustrated?
Get Ahead of the Curve with the Power of Lean Six Sigma
Create Simple, Effective and Efficient Processes that Transform your Business.
Imagine being able to:
- Be more effective without getting busier
- Deliver your product or service to your customers in any circumstances
- Empower your employees to continuously improve your business
- Reduce the amount of overtime put in by you and other employees
- Significantly reduce your operating costs
- Expand your business without impacting productivity
- Solve those chronic, systemic issues in your process operations
Same Business – Less Cost, More Profit.
This program is designed specifically for small to mid-size manufacturing operations.
I’ve lived in your world, trying to optimize processes, reduce costs and safely deliver a quality product but mostly being too busy firefighting and dealing with breakdowns to make any real progress. When you’re expected to deliver results with limited resources, it requires an ability to design clever solutions for persistent process problems.
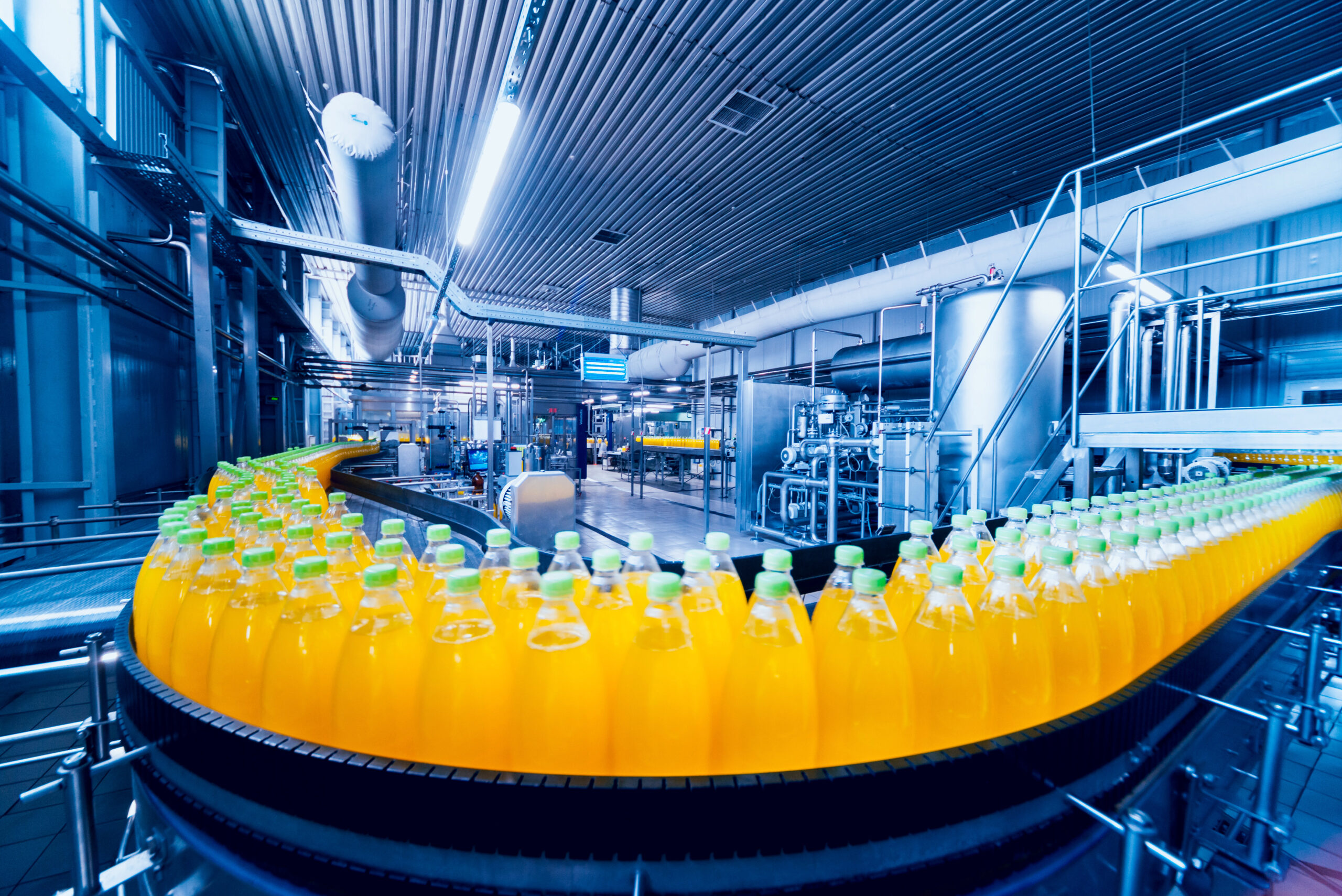
Lean Six Sigma Made Simple
Lean Six Sigma. The name alone just sounds complicated. The truth is, it’s simpler than you think! Lean Six Sigma is a set of tools that create streamlined and highly effective processes that reflect the heart and soul of your business and the difference you’re out to make.
Lean is about streamlining processes and eliminating waste. Six Sigma is about reducing variation in processes. Together Lean Six Sigma works to increase the efficiency, effectiveness and the overall quality of your business processes. With my expert guidance, you won’t go wrong.
Business Processes Typically Contain up to 90% Waste
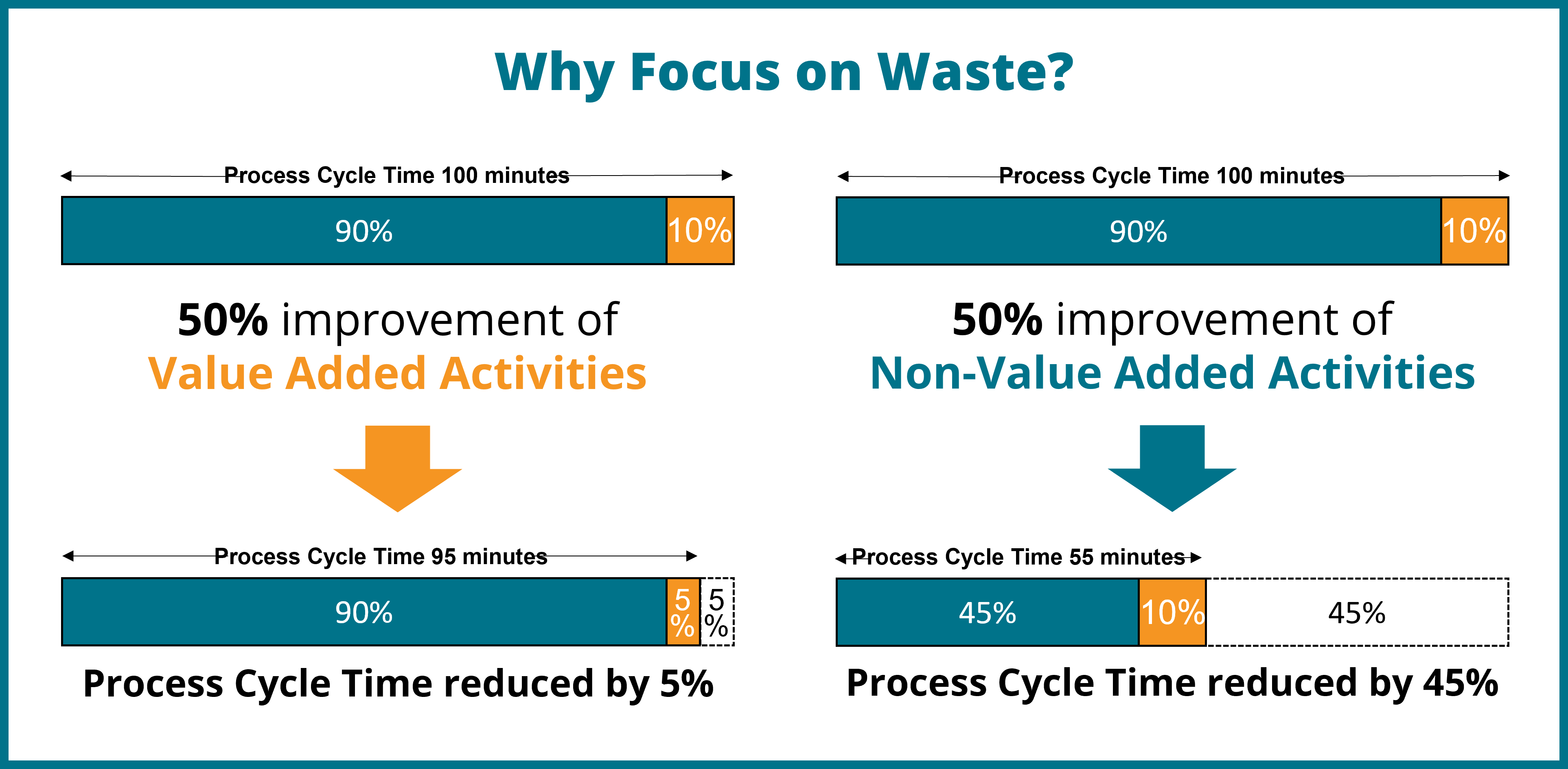
Process Waste includes the activities that consume time, money and resources and don’t add value to your customers – Non-Value Added Activities. The source of your headaches and frustrations, process breakdowns, errors and delays.
The problem is that you don’t often get to the source of the process problems. Instead you get busy trying to manage and address all the symptoms of your problems by adding more time, money and resources. You’ll add inspection processes to deal with product quality issues, increase inventory levels to avoid shortages and accelerate production speed to make more product (like the I Love Lucy chocolate factory). All of these “band-aid solutions” cost money and add to the illusion that the answer to being successful in your business is being able to do more, faster.
It’s a trap.
The Lean Business Assessment
The first step in your Lean Transformation.
I’ll work with you to examine the Current State of your business processes and identify a customized pathway to transform your business into a lean operation – eliminating waste and elevating the performance of your processes.
How It Works
I’ll invest the time to observe your business in action and engage with your front line employees to discover what is working and not working as well as it could be in your business operations. This includes process observations and interviews, data analysis and waste identification. Once my curiosity is satisfied, I’ll prepare a report summarizing the strengths of your business and create the opportunity for process transformation, The report gives you actionable improvements for your business operations and includes a customized proposal for lean consulting and training with Engineering Possibilities.
Your Business Can’t Afford to Wait
It’s time set your business free and create simple, effective and efficient business processes so you can get back to what you do best – running your business.
Your next step is to schedule a conversation with me to discover how completing a Lean Business Assessment can give you the clarity, direction and peace of mind you’re looking for. We’ll identify and prioritize the process improvement opportunities in your business that are critical to your success.
Start by filling out this form to share about your business and how you see that the program can make a difference for your organization. I’ll contact with you to schedule an initial meeting, followed by a proposal customized to your unique needs.
Frequently Asked Questions
What do you know about my business/industry?
You know your business and I know processes. Together we will create the foundation for your continued success and business growth. After working in the chemical processing industry for 9 years I made the leap to healthcare, an industry I literally knew nothing about. The medical speak the doctors and nurses on my project teams engaged in was well over my head, yet the processes they were trying to work with and create were my expertise. Working together, we designed and created processes that enabled their medical procedures and elevated the patient experience. I’m still in the dark about most things medical, but that didn’t stop me from leading several highly successful projects. So regardless of your industry I am confident that we can work together and make a positive impact on your operations.
How does Lean Six Sigma apply to my operation? Isn’t it only for large corporations?
It’s a common myth that Lean Six Sigma only applies to large companies and corporations. Simply put, Lean Six Sigma is a way of making processes simple, effective and efficient – regardless of their size or scope. The definition of a process is “a series of actions designed to produce a particular outcome.” Whether we realize it or not, our lives are filled with processes and there is a great opportunity to streamline the processes in your small business, allowing you to be more effective and productive in your daily activities.
Isn’t Lean Six Sigma only used in Manufacturing Operations?
While most of the Lean Six Sigma tools and concepts were originally derived from the manufacturing industry, the methodology is applicable to any kind of process making it a powerful tool for service and transaction based operations as well as for traditional manufacturing operations.
Lean Six Sigma sounds really complicated, is it too technical for me?
You’re right, Lean Six Sigma does sound really complicated but don’t worry, that’s where I come in. I will work with you to see what’s working and not working in your business and together create simple, effective and efficient processes that enable you to fulfill what matter to you and your customers. I promise it’s simpler than it sounds!
Why do I need to do this now? I’ve got so many competing priorities.
How you run your business is totally up to you. Taking the opportunity to stop and evaluate the performance of your business requires your investment of time and money. We can become blind to what’s not working by being distracted working in our businesses and those activities are required to operate successful, profitable businesses. If you find yourself wondering why things aren’t working as well as you want them to and your strategy of “doing more” isn’t producing the results you’re looking for, then investing in the Lean Business Assessment will give you the competitive advantage you are seeking. There is something to be said about pressing pause on our busy lives to stop and take a look at what areas of our businesses could benefit from some structure and process improvements. Take the opportunity now to get ahead of the curve and discover how Lean Six Sigma can make a difference in your business and what you’re dealing with.
What is the payment structure for the Lean Business Assessment?
The total fee for the Lean Business Assessment is $6,495 + GST. An initial payment of $3,000 + GST is due at the time the consulting contract is accepted and prior to beginning the assessment. Once the assessment is complete, we will provide a summary presentation and the remaining fee of $3,495 + GST is due within 30 days of receipt of the invoice and completion of the assessment.
Why Work with Me?
I’m Holly Blair, I’m a Lean Consultant and the founder of Engineering Possibilities.
I’m a Chemical Engineer with over 12 years of experience in chemical processing, healthcare, service and manufacturing industries.
As a Certified Lean Six Sigma Black Belt, Change Management Practitioner and Certified Executive Coach, I provide an innovative approach to process improvement by integrating Systems Thinking with Lean Methodologies. I am an engaging facilitator of Lean Training Workshops and Kaizen Events that leave my Clients empowered with the capability to create lean process improvement results in your own environments. I have a knack for distilling your processes down to what really works, creating ease and simplicity in otherwise chaotic and complex environments.
Capture Your Current State and Create What’s Possible
What you get with the Lean Business Assessment:
- Summary Report outlining the Current State of the Performance of your Business Operations
- Lean Transformation Action Plan
- Electronic Process Maps and Documentation
- Quick Win Process Improvement Opportunities
- Improved Process Reliability, Elevated Efficiency and Cost Savings
- Clarity, Direction and Peace of Mine around your Business Operations
- Renewed Focus on the Growth & Expansion of Your Business
It’s time to take control of your business and design effective systems and processes that empower your business to make the difference you want to make for your customers. Click below to complete the Lean Business Assessment Request Form and start your Lean Transformation today.